Carbonschäfte sind im modernen Bogensport heute nicht mehr wegzudenken und daher auch im 3D-Bogensport und insbesondere bei uns traditionellen Bogenschützen seit vielen Jahren auf dem Vormarsch. Es gibt mittlerweile dutzende Hersteller und hunderte verschiedener Carbonschaftmodelle auf dem Markt, sodass viele hier den Überblick verlieren.
Jeder Hersteller preist dabei – wie soll es auch anders sein – selbstverständlich seine Modelle als die Besten auf dem Markt an. Sie seien stabiler als andere, mit weniger Toleranzen gefertigt, nach Gewicht sortiert, ihr Spine innerhalb engster Grenzen, ein „Spline“ sei nicht vorhanden und viele andere Versprechungen werden dabei gemacht.
Was hier wirklich richtig ist und nicht nur substanzloses Marketinggebrabbel, lässt sich für den Otto-Normal-Schützen nicht bis kaum überprüfen, weil ihm dazu die entsprechenden Messgeräte fehlen und Angaben wie „stabiler als andere“ meist nur subjektive Eindrücke sind.
Außerdem müsste man repräsentative und wiederholbare Tests durchführen, um die Angaben überprüfen zu können. Das kostet Zeit und Geld. Meines Wissens nach wurden solche groß angelegten Tests bislang noch von niemandem durchgeführt. Insofern können wir darauf nicht zurückgreifen.
Es stellt sich also die Frage, ob man aus den Herstellerangaben ggf. Rückschlüsse auf die Art der Herstellung, verwendete Materialien und damit auch auf die Qualität der Pfeilschäfte ziehen kann.
Und um uns dieser Frage zu nähern, schauen wir uns zunächst einmal an, welche Materialien bei der Herstellung verwendet werden, welche Möglichkeiten hinsichtlich des inneren Aufbaus eines Schafts es gibt und wie Carbonschäfte letztlich in der Praxis industriell hergestellt werden.
Verwendete Materialien
Alle Carbonschäfte bestehen – wer hätte es auch anders erwartet – aus Carbon, also Kohlefasern und aus einem Klebstoff (in der Regel Epoxidharz), der die Fasern zusammenhält. Es gibt dabei Schäfte, die zu 100% aus mit Epoxidharz „verklebten“ Kohlestofffasern bestehen und solche, die zusätzlich auch z.B. Fiberglas enthalten, um zusätzliches Gewicht einzubringen.
Erstere werden in Produktbeschreibungen und Werbetexten meist als „100% Carbon“ bezeichnet, bei Schäften die Fiberglas enthalten liest man dagegen eher gar keine Angabe über das Material.
Die Kohlefasern, die zur Herstellung verwendet werden, werden in Faserbündeln (sog. Tows) auf Spulen von den Carbonfaserherstellern bereitgestellt. Je nachdem, wie viele Fasern diese Bündel enthalten, spricht man von 1K, 3K, 6K, 12K usw.
Ein 1K Tow hat also 1000 Fasern, das 3K 3000 Fasern und das 6K 6000 Fasern. Je mehr Fasern ein solches Bündel hat, desto dicker ist es auch und erzeugt z.B. bei einem Carbongewebe unterschiedlich große Muster (Rauten).
Ob ein Schaft aus 1K, 3K oder 6K hergestellt ist, sagt nichts (!) über die Qualität der Carbonfasern aus, sondern lediglich etwas über die Dicke des Grundmaterials zur Herstellung und die Größe eines eventuell entstehenden Musters aus. D.h. es ist ggf. lediglich als eine Angabe zur Optik tauglich, sofern die äußerste Schickt eines Schafts ein entsprechendes Gewebe darstellt.
Die nachfolgende Abbildung soll die Größenunterschiede von 1K bis 12K Tows bei einem Gewebe in sog. 2×2 Twill verdeutlichen:
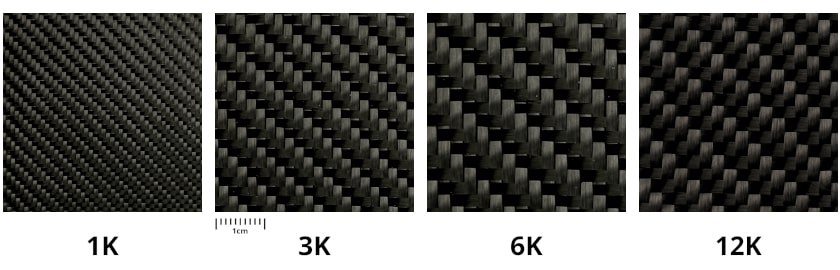
Der innere Aufbau von Carbonschäften
Der Aufbau eines Carbonschafts, also die Lage der Carbonfasern bzw. der einzelnen Schichten und auch deren Verlauf, hängt sehr stark vom Herstellungsverfahren ab, mittels dessen der Carbonschaft produziert wird. Grundsätzlich gibt es hinsichtlich des Verlaufs der Fasern drei mögliche Richtungen.
- Entlang des Schafts (0°)
- Helikal, also spiralförmig um den Schaft herum (1°-89°)
- Quer zum Schaft (90°)
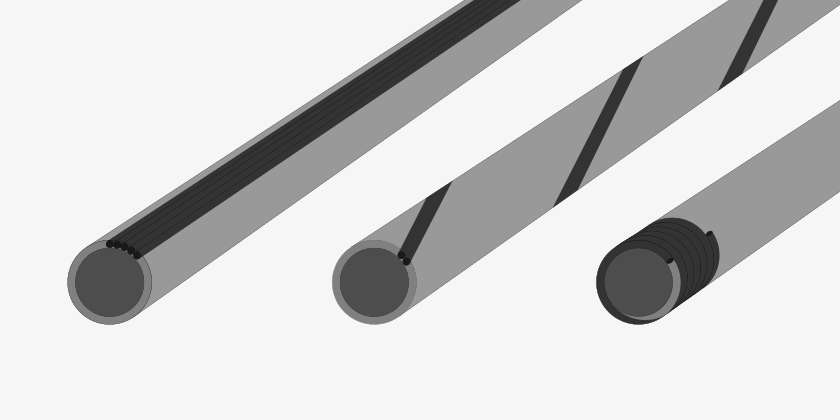
Die Abbildung soll nur die verschiedenen Faserveraufsrichtungen darstellen!
Der Faserverlauf entlang des Schafts sorgt für eine hohe Biegesteifigkeit, der Verlauf quer zum Schaft für eine hohe Druckstabilität und der helikal um den Schaft herumgewundene Verlauf – insbesondere wenn er in verschiedenen Winkeln erfolgt – für eine sehr hohe Torsionssteifigkeit.
Die meisten heutigen Carbonschäfte enthalten Fasern in allen drei der o.g. Grundrichtungen, um alle drei Eigenschaften sicherzustellen. Der Großteil der Fasern wird vermutlich entlang des Schafts verlaufen, da die Biegesteifigkeit die wichtigste der drei Eigenschaften für den Bogensport ist.
Die Schäfte bestehen dabei aus mehreren Lagen von Fasern und Faserrichtungen, sodass eine Lage entlang des Schafts beispielsweise von einer helikal verlaufenden Lage überdeckt wird und sich darauf wiederum eine Quer zum Schaft verlaufende Faserlage befinden kann, usw.
Manche Hersteller warben in der Vergangenheit sogar damit, dass sie an den beiden Enden der Schäfte die Fasern in anderen Winkeln oder mehr Fasern quer oder helikal verlaufen lassen, um die Enden ihrer Schäfte stabiler zu machen. Insbesondere Werbeaussagen in dieser Richtung von GolpTip sind mir noch in Erinnerung. Allerdings konnte ich trotz ausgiebiger Recherche keinen Hersteller mehr finden, der heutzutage entsprechende Aussagen trifft. Lediglich ein US-Patent aus dem Jahr 1999 deutet noch darauf hin (siehe hier).
Für uns als Händler und dich als Kunde ist es nicht möglich, den inneren Aufbau des Schafts von außen zu beurteilen. Die meisten mattschwarzen Carbonschäfte haben beispielsweise als äußerste Lage einfach nur einen entlang des Schafts verlaufenden Faserverlauf (sofern die äußere Schicht nicht bewusst vom Hersteller schwarz Matt lackiert wurde). Dies lässt aber keine Rückschlüsse darauf zu, wie der Aufbau des Schafts darunter ist.
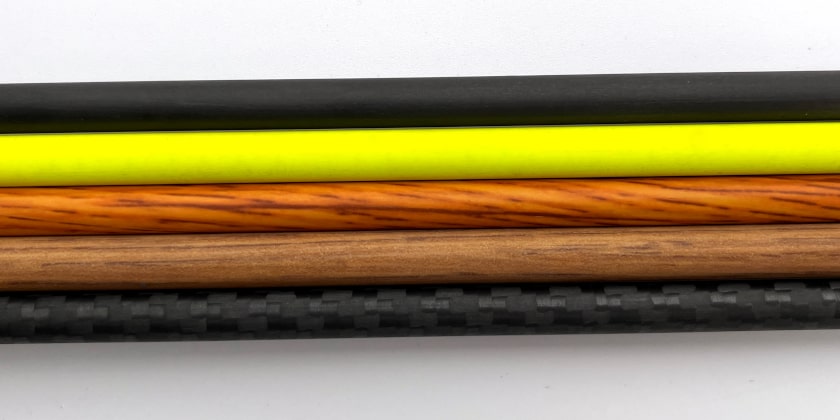
Gleiches gilt z.B. für Schäfte, bei denen außen klar eine „Gewebestruktur“ erkennbar ist. Egal ob 3K oder 1K 2×2 Twill, auch hier hat sich der Hersteller einfach nur zum Erreichen einer bestimmten Optik für eine entsprechende äußere Lage an Fasern/Gewebe entschieden. Bei Schäften mit farbig lackierter Oberfläche oder „Holztapete“ ist natürlich auch nichts von außen erkennbar.
Der grundsätzliche Herstellungsprozess eines Carbonschafts
Ein Carbonschaft ist letztlich nichts anderes als ein Rohr aus Kohlefaser und wird daher mit den für diese Rohre üblichen Verfahren industriell hergestellt. Welche Verfahren die einzelnen Hersteller verwenden, daraus wird zum Teil regelrecht ein Geheimnis gemacht. Aber niemand kann das Rad neu erfinden!
Grundsätzlich gibt es für die Massenfertigung von Carbonrohren nach meinen Recherchen vier Verfahren, die zur Anwendung kommen können. Diese wollen wir uns nun einmal genauer ansehen. Diese sind:
- Filament Winding
- Prepreg Roll Wrapping
- Pultrusion
- Pullwinding
Beim Filament Winding werden die Carbonfaserbündel durch ein Expoxidharzbad gezogen und um eine rotierende Welle (sog. mandrel) gewickelt. Die Richtung der Fasern wird dabei von einem „fahrenden Schlitten“ nach einem vordefinierten Muster abgefahren. Dieses Verfahren ist sehr zeitaufwändig, erlaubt aber fast jeden beliebigen Winkel der Fasern, außer exakt in Längsrichtung zum „Rohr“.
Beim Prepreg Roll Wrapping wird ein vorher bereits hergestelltes und vorab mit Harz getränktes Faser-Gewebe (prepreg = engl. preimpregnated), das aus mehreren Lagen verschieden angeordneter Carbonfaserrichtungen bestehen kann, unter Druck ebenfalls um eine Welle gewickelt.
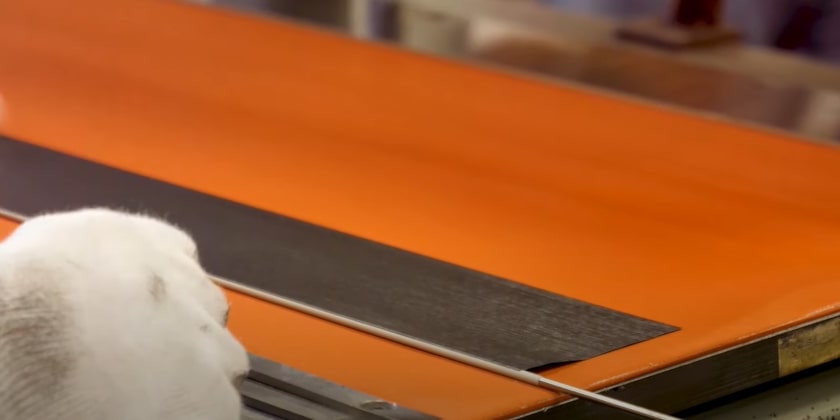
Mandrel und Prepreg-Gewebe bei der Herstellung eines Carbonschafts mittels Prepreg-Roll-Wrapping-Verfahren
In diesem YouTube-Video werden die beiden Verfahren darstellt:
https://youtu.be/Yv_SNdwQPl4?t=6
Pultrusion und Pullwinding sind beide sehr ähnliche Verfahren. Bei beiden werden Carbonfaserbündel zunächst durch ein Expoxidharzbad und dann durch eine Art (Press-)Form gezogen, sodass am Ende ein „Endlosrohr“ in den gewünschten Dimensionen entsteht, das letztlich auf die gewünschten Längen gekürzt wird.
Der Unterschied zwischen dem „normalen“ Pultrusions-Verfahren und der besonderen Art von Pultrusion, dem Pullwinding-Verfahren, ist, dass bei der Pultrusion normalerweise die Fasern nur in eine Richtung, also entlang der Fertigungsrichtung (=entlang des Rohrs) verlaufen. Beim Pullwinding kann es sowohl Fasern in Längsrichtung geben, als auch Schichten von Fasern, die helikal um das Rohr herum oder zumindest annähernd quer zur Längsrichtung verlaufen.
Dieses Video zeigt u.a. diese beiden Verfahren: https://www.youtube.com/watch?v=o9FvUWSOeNc
Welche Verfahren werden heutzutage angewandt?
Die ersten auf dem Markt erhältlichen Carbonschäfte wurden alle im Pultrusionsverfahren hergestellt und hatten ausschließlich in Längsrichtung angeordnete Fasern. Das machte sie jedoch nicht besonders Druckstabil und sie splitterten im Falle eines Bruchs ziemlich stark auf, weshalb Carbonschäfte anfangs als sehr gefährlich galten. Im Schaftinneren liegende Komponenten wie die heutigen Klebeinserts oder Push-In-Nocken waren wegen der fehlenden Druckstabilität damals nicht verwendbar. Stattdessen mussten Nocken immer außen über den Schaft ragen und auch Spitzen entweder am Schaft überstehen oder zumindest Inserts mit Outserts verwendet werden. Heute werden kaum noch Schäfte in diesem sehr günstigen Verfahren hergestellt, allenfalls extrem billige Carbonpfeile. Von einer Verwendung solcher Pfeile ist wegen der hohen Verletzungsgefahr auch abzuraten.
Filament Winding wurde für die Massenfertigung von Carbonschäften nie eingesetzt, da die Durchmesser von Carbonschäften für die meisten Anlagen viel zu klein sind und durch den großen Zeitbedarf zur Herstellung, die Schäfte extrem teuer wären.
Heute werden nur die beiden Verfahren Prepreg Roll Wrapping und Pullwinding für die Herstellung von Carbonschäften eingesetzt.
Welcher Hersteller sich dabei welchen Verfahrens bedient, daraus machen die meisten Marken ein riesiges Geheimnis. Aber zumindest für einige Hersteller und Carbonschafttypen konnte ich aufgrund der Produktbeschreibungen, diverser Videos und Informationen der Herstellerwebseiten deren Herstellungsverfahren bestimmen. Dazu aber weiter unten mehr.
Ist eines der beiden Verfahren besser als das Andere?
Beim Prepreg Roll Wrapping kann das um die metallische Welle gewickelte Carbonfasergewebe Fasern in jede beliebige Richtung (0-90°) enthalten und auch so gestaltet sein, dass bestimmte Bereiche des Schafts mehr Fasern einer bestimmten gewünschten Ausrichtung haben, als andere Bereiche. Zudem ist das Verfahren durch den hohen Anteil an menschlicher Arbeit und der Herstellung in Billiglohnländern relativ günstig und so hergestellte Schäfte dann am Ende auch eher am unteren Ende des Preissegments anzusiedeln.
Nachteil des Verfahrens ist, dass durch das Aufwickeln des vorbereiteten Gewebes an einer Stelle der Anfang und an einer anderen Stelle das Ende des Gewebes sein muss. An diesen Stellen weicht der Spinewert vom Rest des Schafts etwas ab und der Schaft ist dort steifer, als an anderen Stellen entlang seines Umfangs. Diese steifen Stellen werden oft auch als „Spline“ oder „Nahtstelle“ bezeichnet. Für ein 100%ig exaktes Pfeiltuning ist es bei so hergestellten Schäften in der Regel nötig die Schäfte nach ihrem Spinewert beim Pfeilbau exakt auszurichten. Man spricht dann auch von Spine-Alignment. Bei dem Verfahren ist es auch nötig, dass das außen liegende Ende des Gewebes noch verschliffen wird, sodass der Übergang nicht mehr sichtbar ist und der Schaft möglichst rund wird.
Die mittels Pullwinding hergestellten Schäfte sind durch den hohen Automatisierungsgrad und die dafür erforderlichen und aufwendigen Maschinen teurer, aber durch den automatisierten Endlosprozess wesentlich genauer in Sachen umlaufender Spine-Konsistenz, Rundheit und Gleichheit von Schaft zu Schaft.
Aus der Sicht eines traditionellen Bogenschützen der hauptsächlich auf 3D-Parcours unterwegs ist und insbesondere wenn er instinktiv schießt, sind Schäfte, die mittels Prepreg-Roll-Wrapping hergestellt werden, absolut ausreichend. Sehr gute Schützen oder sehr ambitionierte Personen, die das absolute Maximum aus ihrem Material herauskitzeln wollen, für die sind vermutlich die in Summe genaueren und gleichförmigeren Schäfte, die mittels Pullwinding-Verfahren hergestellt werden, die bessere, aber dann natürlich auch teurere Wahl.
Welcher Hersteller stellt nach welchem Verfahren her?
Wie bereits weiter oben angedeutet, halten sich die meisten Hersteller sehr bedeckt, was den Herstellungsprozess ihrer Carbonschäfte anbelangt. Das nicht nur, um Mitbewerbern den eigenen, möglicherweise innovativen Prozess zu verheimlichen, sondern vermutlich auch, um die Kunden nicht zu irritieren.
Wenn man unter Bogenschützen z.B. die Frage stellt, wie Carbonschäfte hergestellt werden, dann stellen viele sich ein Verfahren wie das oben beschriebene Filament Winding vor. Da die meisten Schäfte per Prepreg-Roll-Wrapping hergestellt werden, ist ziemlich genau das Gegenteil von der Vorstellung der allermeisten Schützen der Fall.
Zu einigen Herstellern und Schäften konnte ich mit etwas Aufwand Aussagen und Informationen zum Herstellungsprozess recherchieren:
Schäfte von Victory Archery zum Beispiel werden mittels Prepreg Roll Wrapping Verfahren gefertigt. Darauf deutet ein Interview des General Managers von Victory Archery Stephen Greenwood aus Januar 2020 hin, in welchem er sagt: “Because of the way a carbon arrow is made, there is a section of the arrow that is distinctively stiffer[.] […] all of our arrows are spine aligned, meaning that stiffer section is marked during that process. […]” (Quelle: https://us.mitsubishi-chemical.com/victory-archery-a-winning-mentality/)
Easton stellt alle seine Carbonschäfte nach einem Verfahren her, das sie als „Acu-Carbon-Technology“ bezeichnen. In einem auf YouTube veröffentlichen Video teilt der stellvertretende Betriebsleiter von Easton in Salt Lake City (UT) Clay Henderson mit: „We have over 30 pultrusion machines [that produce] all carbon arrows. […] This ist he way we produce it. […] other manufacturers they’ll roll it and we pultrude it.“ (Quelle: https://youtu.be/pvRwWmzPu1U?t=145)
Obwohl er in dem Video von Pultrusion spricht, sieht man im weiteren Verlauf deutlich, dass Faserbündel auch rotierend eingezogen werden und es sich also um Pullwinding handeln muss.
Auf der Easton-Webseite steht zudem „Ordinary, wrapped carbon shafts suffer from […] spine inconsistency and weight variation […]. Easton’s Acu-carbon arrows use a unique seamless shaft winding process that results in a more consistent product that is a cut above typical hand-rolled carbon shafts. […] [This] process is a continuous-fed, single-die manufacturing method that results in the more reliable tolerances, eliminating the need for spine-alignment and weight sorting.“ (Quelle: https://eastonarchery.com/2022/05/acu-carbon-arrow-construction-how-arrows-are-made/) Auch das deutet darauf hin, dass nicht per Prepreg Roll Wrapping produziert wird, sondern Pullwinding.
Der Hersteller Aurel Archery schreibt auf seiner Webseite bei einigen Schäften, wie z.B. dem AGIL oder UHYRE recht offen und deutlich, dass seine „Schäfte aus 100% […] Carbon-Prepregs [bestehen]“ (Quelle: http://aurel-archery.de/pfeilschaefte/aurel-schaft-spezifikationen/) D.h. hier wird per Prepreg Roll Wrapping gefertigt.
Bei GoldTip findet man leider keine Hinweise auf ein mögliches Herstellverfahren. Man hält sich sehr bedeckt.
Bearpaw hat für seine Penthalon-Schäfte vor geraumer Zeit einmal ein Video online gestellt, das den Herstellungsprozess mittels Prepreg Roll Wrapping zeigt. Leider ist dieses Video aktuell nicht mehr auffindbar. Für diesen Herstellungsprozess, zumindest bei dem Schaft Penthalon Hunter Extreme, spricht dessen äußere Optik, die ein 3K 2×2 Twill Gewebe zeigt und auch mindestens eine Stelle entlang des Umfangs hat, welche verschliffen ist.
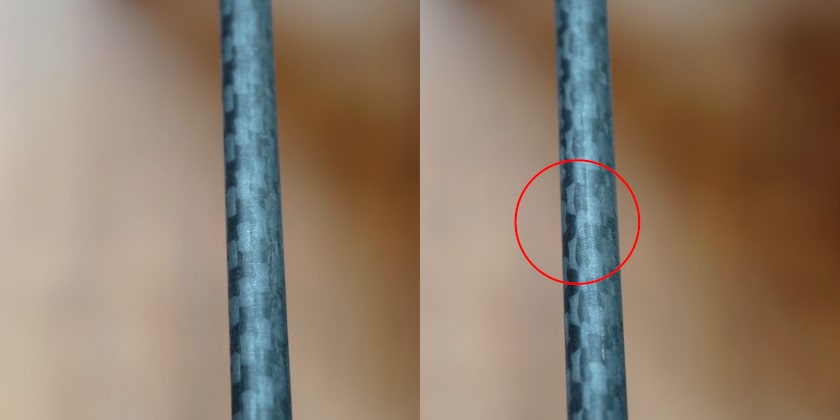
Rechts sieht man – im Gegensatz zum Bild links – eine Unregelmäßigkeit im Muster des Gewebes. Dies ist die „Nahtstelle“.
Eine solche Gewebeoptik lässt sich ausschließlich mit Prepreg Roll Wrapping erzeugen und sonst mit keinem anderen der o.g. Verfahren.
Der Hersteller Nijora ist in Sachen Produktbeschreibung teilweise etwas widersprüchlich oder zumindest unklar in Bezug Material und auch auf Beschreibung der Herstellungsweise. Beim Carbonschaft Elsu Pro wird beispielsweise von einer „spezielle[n] Linear Wicklung bestehend aus mehrlagigem Carbon Layer Geweben“ und von „handgeschliffen“, sowie von „100 % Carbon in 8 Lagen Kreuzwickeltechnik hergestellt“ gesprochen. (Quelle: https://nijora.com/elsu-pro/) Beim Schaft 3K Pro wird von „Edel 3 K Carbon“ und „100 % Carbon in 6 K tranzial Kreuzwickeltechnik hergestellt“ (Quelle: https://nijora.com/3k-pro/) gesprochen. Ja, auch ich habe mich nach dem Lesen direkt gefragt.. „Na was denn nun?“. Aufgrund der Optik, insbesondere des 3K Pro und der Beschreibung beim Elsu Pro, ist aber davon auszugehen, dass Nijora ebenfalls mit Prepreg Roll Wrapping herstellen lässt.
Die Schäfte von Henry Bodnik Partizan Extreme und Barracuda werden nach Angaben von Henry ebenfalls nach dem Prepreg Roll Wrapping Verfahren hergestellt. Insbesondere beim Partizan Extreme ließe sich dessen Optik, wie auch schon die des Nijora 3K Pro oder Penthalon Hunter Extreme, nicht anders erzeugen.
Welche Schlüsse kannst du nun aus den gewonnenen Erkenntnissen ziehen?
Du kennst nun die Verfahren, mit denen Carbonschäfte hergestellt werden können, deren Vor- und Nachteile und ich habe auch einige Hinweise geliefert, wie die gängigsten Hersteller und Marken ihre Schäfte produzieren.
Zum einen kann man festhalten, dass im Pullwinding-Verfahren hergestellte Carbonschäfte tendenziell gleichmäßiger und mit weniger Fertigungstoleranz gefertigt werden können als im Prepreg-Roll-Wrapping-Verfahren. Das heißt, würden die Hersteller nach der Produktion auf ein Messen und Sortieren der Schäfte nach Spinewert, Rundlaufgenauigkeit und Gewicht verzichten, dann wäre die Qualität in Bezug auf die Toleranzen der im Pullwinding-Verfahren hergestellten Schäfte etwas besser.
Jedoch kontrollieren und sortieren die Hersteller natürlich Ihre Schäfte nach der Fertigung und sortieren diese ggf. auch aus, wenn die Toleranzen zu groß sind. Uns bleibt als Schützen letztlich nur die Möglichkeit entweder Schäfte zu kaufen, bei denen die angegebenen Toleranzen möglichst klein sein sollen und darauf zu vertrauen, dass das, was die Hersteller behaupten, auch stimmt oder wir müssen eben nachmessen und eine eigene Sortierung der gekauften Schäfte nachträglich vornehmen. Aus dem Herstellungsverfahren selbst lässt sich allenfalls eine Tendenz ableiten.
Was die Stabilität eines Carbonschafts anbelangt, gibt es grundsätzlich kein Verfahren, das hier per se Vorteile bietet. Die Robustheit eines Schafts hängt vor allem von der Menge und Wickelrichtung der verwendeten Kohlefasern ab und dies unabhängig vom Verfahren. Man kann aber sagen, dass ein leichter Schaft mit größerem Innendurchmesser tendenziell weniger stabil ist als ein schwererer Schaft mit kleinerem Innendurchmesser. Der Grund liegt in der Wandungsstärke des Schafts.
Zudem darf man auch nicht außer Acht lassen, dass die Qualität der Verklebung von Spitze und Insert beim Pfeilbau und ob der Carbonschaft sachgerecht mittels Trennscheibe abgelängt wurde auch wesentlichen Einfluss auf die Haltbarkeit eines Schafts haben kann. Wer hier also Fehler macht, kriegt auch den stabilsten Schaft bei einem nur etwas härteren Treffer zum Bersten.
Du hast Anmerkungen oder Fragen?
Falls du Fragen zu unserem Blogartikel hast oder eine Anmerkung machen möchtest, freuen wir uns natürlich, wenn du dich bei uns meldest!
Entweder schreibst du uns einfach eine Nachricht über das unten stehende Kontaktformular oder kontaktierst uns per Mail oder Facebook. Hier findest du unsere Kontaktdaten.
Du hast Anmerkungen oder Fragen?
Falls du Fragen zu unserem Blogartikel hast oder eine Anmerkung machen möchtest, freuen wir uns natürlich, wenn du dich bei uns meldest!
Entweder schreibst du uns einfach eine Nachricht über das unten stehende Kontaktformular oder kontaktierst uns per Mail oder Facebook. Hier findest du unsere Kontaktdaten.
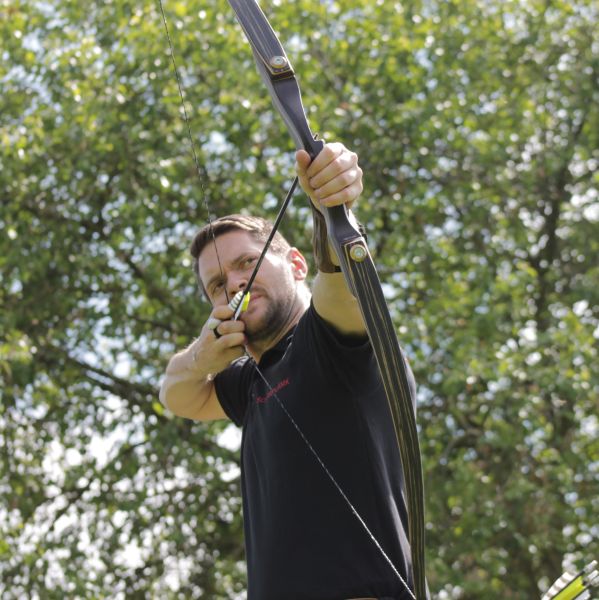
Daniel Goll
Vor mittlerweile fast 25 Jahren entdeckte er den Bogensport und insbesondere das Traditionelle Bogenschießen für sich und hat bei zahlreichen Turnieren, Wettkämpfen und Meisterschaften geschossen. Daniel ist zertifizierter Trainer im Instinktiven Bogenschießen der Instinktive Archery Academy (IAA) und hat über die Jahre hinweg viele Bogenschützinnen und Bogenschützen bei ihrem Einstieg in das Bogenschießen, dem Erlernen des instinktiven Bogenschießens und im Einzeltraining zur Fehleranalyse und Fortentwicklung unterstützt.